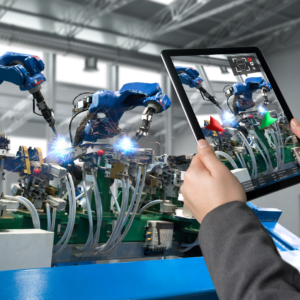
This use case pertains to use of AR-assisted systems to diagnose issues and, once issues identified, provide digital assets and visual instructions to the user when performing repair and maintenance tasks. There is some overlap with inspection, remote assistance and complex assembly use cases.